Several common transfer methods in transfer printing
July 4, 2025
Transfer printing is a widely used technique in cosmetic packaging, allowing for high-quality decoration on various substrates. Here are the main types of transfer printing methods.
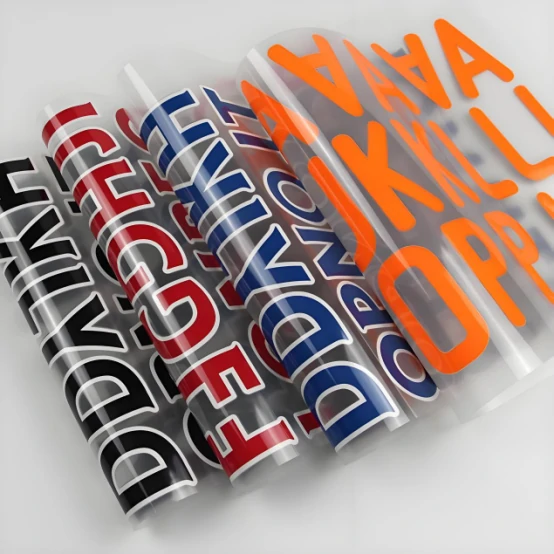
Transfer Printing
Transfer printing is a technique where graphics or text on an intermediate carrier are transferred onto a substrate using pressure. This method is particularly useful for irregular, pre-formed, or flexible materials that cannot be printed directly on conventional presses. The image is first printed onto a transfer medium (e.g., special paper or film) and then transferred to the substrate through heating, moistening, or pressure.
01. Classification by Transfer Method
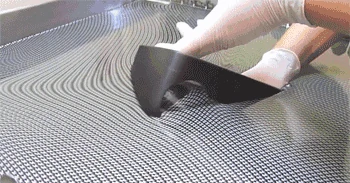
Based on the pressure application, transfer printing can be divided into:
Heat Transfer – Uses temperature to melt the adhesive layer on the transfer film, applying pressure for transfer.
Water Transfer – Relies on water pressure and activators to dissolve the release layer for transfer.
Gas (Sublimation) Transfer – Uses gas pressure to sublimate dye-based inks onto the substrate.
Screen Transfer – Applies adhesive to the substrate first, then uses a squeegee to transfer the image.
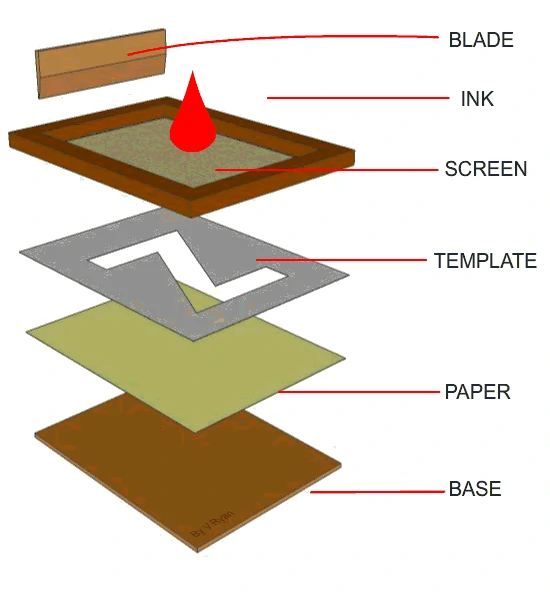
By Ink Type: Heat Press Transfer and Dye-Sublimation Transfer
By Substrate: Fabrics, Plastics (sheets, films), Ceramics, Metal-coated boards
By Printing Method: Screen printing, Lithography, Gravure, Flexography, Inkjet, Ribbon Printing
By Transfer Medium: Transfer Paper, Transfer Plastic Film
02. Heat Transfer VS Water Transfer
1) Heat Press & Dye-Sublimation Transfer
Heat Press Transfer: The image is first printed onto transfer paper/film and then heat-pressed onto fabrics, leather, etc.
Dye-Sublimation Transfer: Uses sublimation inks printed on transfer paper, which are then heated to turn into gas and bond with polyester-based materials (e.g., fabrics, ceramics, metals).
2) Water Transfer
Water transfer involves a special water-soluble film as the carrier. The film dissolves in water, allowing the design to adhere to the substrate without heat or pressure—ideal for heat-sensitive or ultra-thin materials.
Water Decal Transfer: For text and detailed graphics.
Hydrographic (Water Immersion) Transfer: Covers the entire product surface, creating a seamless, painted-like finish.
Currently, heat transfer and water transfer are the most widely used methods. However, water transfer offers broader applications and greater market potential.
03. Film Transfer VS Sublimation Transfer
Film Transfer: Uses transfer paper with a glue layer, applying heat and pressure to bond the design.
Sublimation Transfer: Uses special sublimation inks and paper, where heat converts the ink into gas for permanent transfer.
04. Screen Printing VS Digital Transfer
Screen Printing: Relies on overprinting and halftone dots for color gradients, limiting high-resolution photo reproduction.
Digital Transfer: Uses computer-designed images printed onto transfer paper via digital printers, then heat-pressed onto substrates. Ideal for detailed, photorealistic prints.
05. Direct VS Indirect Transfer Printing
Direct (Pad Printing): A silicone pad picks up ink from an etched plate and stamps it onto 3D surfaces (e.g., plastic caps, tubes). Curing is done via heat or UV light.
Indirect (Transfer Paper Printing): Uses a multi-layered transfer paper (base, ink, adhesive).
More complex and costly for small batches but ensures high precision, durability, and low defect rates.
Learn more:sublimation machine supplier;automatic heat press;transfer paper,etc.
Have any other questions? Welcome to contact us!